
Buscando maior produtividade, empresas substituem o ferro e o aço na fabricação de peças e componentes na fabricação de máquinas agrícolas
POR GUSTAVO PAES
Desde o seu surgimento, as máquinas e os implementos agrícolas evoluíram muito. Nas últimas décadas, as inovações foram possíveis, em grande parte, devido a mudanças nos materiais utilizados pela engenharia.
Até pouco tempo, as máquinas agrícolas que rodavam nas nossas lavouras não passavam de umas caixas quadradas, construídas exclusivamente de aço e ferro fundido. Porém, isso vem mudando rapidamente e a indústria de máquinas agrícolas segue um rumo parecido com o de outras indústrias, como a aeronáutica e a automobilística, que também tiveram seu desenvolvimento impulsionado pela utilização inovadora de materiais. Hoje, o maquinário agrícola é produzido com diferentes materiais, como plásticos, ligas de alumínio e compósitos. A cada dia surgem novas alternativas e as opções disponíveis aos projetistas se expandem cada vez mais. Como a impressão 3D, adotada, por exemplo, pela CNH Industrial, Stara e Cummins para desenvolver protótipos. Mas o que levou a indústria a apostar na substituição do metal na fabricação de determinadas peças por plásticos ou outros compostos?
Os especialistas apontam várias razões para o uso de diferentes materiais nas máquinas agrícolas. Em alguns csos, o projeto com peso leve é quase uma obrigação devido a normas legais e também para evitar a compactação do solo, um problema que afeta diretamente o desenvolvimento e a produtividade das culturas na lavoura. Outros motivos seriam o aumento da demanda no tempo de vida das máquinas e os requisitos de design e ergonomia do maquinário.
O fato é que a abertura de novas áreas em regiões com potencial produtivo e a redução das janelas de plantio e colheita exigem que o produtor precise de um conjunto máquina-implemento com maior potência operacional. Com a demanda do agricultor por máxima produtividade, os tratores e as colheitadeiras ganharam mais tecnologia embarcada e aumentaram de potência e tamanho. No entanto, máquinas maiores provocam compactação do solo e aumento do consumo de combustível.
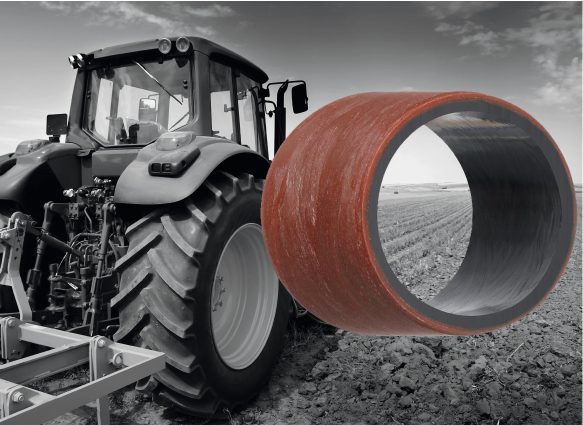
Continue lendo sobre esse assunto
MATERIAIS LEVES
A utilização de materiais leves, que possibilitem o projeto de máquinas maiores, porém, não tão pesadas, é uma alternativa para amenizar esse problema. Os fabricantes sabem que um equipamento mais leve ajuda a preservar o solo e sua produtividade. Mas o desafio para a indústria é que os materiais que produzem as peças mais leves, com ótimo acabamento e alta resistência são, geralmente, os mais caros.
A introdução de materiais leves em substituição aos tradicionais como o aço é uma realidade neste setor. Todas as famílias de materiais de engenharia são utilizadas na construção das máquinas agrícolas atuais. Os materiais compósitos, leves e de alta performance, vêm se destacando como importantes aliados no aumento da eficiência e na redução da massa destes equipamentos.
Porém, na contramão da substituição dos aços por compósitos, os metais vêm evoluindo e também têm acompanhado a tendência de redução da massa e aumento de resistência. A utilização de aços de alta resistência em máquinas e implementos permite a redução nas espessuras e consequente redução de massa nos produtos. Porém, o aumento da resistência dos aços traz inevitavelmente maiores desafios para a fabricação.
Ainda houve evolução nas técnicas de revestimento, que reabririam o caminho para o uso de aços carbo-no em aplicações em que se exige resistência à corrosão.
GRAFENO
O especialista em mecanização agrícola do Serviço Nacional de Aprendizagem Industrial (Senai-RS), Joel Sebastião Alves, destaca que empresas de máquinas agrícolas da Serra Gaúcha já estão utilizando o grafeno, um material que foi isolado pela primeira vez em 2004, na Inglaterra, pelos cientistas Andre Geim e Konstantin Novoselov, e é considerado o futuro da tecnologia.
O grafeno é quase transparente, leve, maleável, resistente ao impacto e à flexão, além de ser um excelente condutor de calor e eletricidade. É 200 vezes mais resistente do que o aço, superando até mesmo o diamante. Uma folha de grafeno de 1 metro quadrado pesa 0,0077 gramas e é capaz de suportar até quatro quilos.
“O grafeno está sendo utilizado na fabricação de carcaças, do bloco do motor e da caixa de máquinas agrícolas”, destaca Alves. “O emprego do material, que é muito mais leve e resistente, aumenta o rendimento, reduz o consumo de combustível e ainda diminui a compactação do solo”, acrescenta.
Desde março de 2020, funciona em Caxias do Sul (RS), a UCS Gra-phene, a primeira e maior planta de produção de grafeno em escala industrial da América Latina instalada
por uma universidade (Universidade de Caxias do Sul). A unidade tem capacidade de produzir 5 mil quilos ao ano, estando apta a abastecer os mercados nacional e internacional com grafeno de alta qualidade. “Inúmeras são as empresas e soluções que foram ou que estão sendo desenvolvidas fazendo uso das nanoplaquetas de grafeno que são produzidas em nossa planta”, diz Daniele Perondi, especialista em Pesquisa e Desenvolvimento na USC Graphene, que tem parceria com mais de 200 empresas de diferentes setores, segundo ela.
MAIS LEVES E RESISTENTES
Desde 2021, a fabricante de peças plásticas rotomoldadas Giroplastic utiliza a inovação em alguns de seus processos de produção, em parceria com diferentes clientes, de setores como o moveleiro, agrícola e automobilístico. Ao processo mais antigo de transformação do plástico, a rotomoldagem, a inovação do uso do grafeno agrega na geração de peças mais fi nas, mas com a mesma resistência, e na redução do tempo de processo produtivo por suas qualidades condutoras.
A Giroplastic produz defl etores e tanques, de 800 e 1000 litros, para pulverizadores da Rubemaq. A empresa também estuda utilizar o grafeno no revestimento de tanques de combustível de máquinas pesadas. “O foco do uso do grafeno é reduzir o peso e aumentar a resistência das peças das máquinas agrícolas”, salienta a diretora de Desenvolvimento de Projetos, Elisa Mazzotti Schmitz.
Os defl etores produzidos pela empresa utilizando o novo material são bem mais leves que os produtos oferecidos no mercado. “Um defl etor grande, fabricado em fi bra de vidro, pesa em torno de 60 quilos. Os nossos, 16 quilos. Isso reduz o peso da máquina e permite uma maior economia de combustível”, destaca a executiva. O objetivo, agora, é encontrar uma maneira de usar o grafeno e equilibrar os custos de produção, já que a grama do material é comercializada, em média, por US$ 100 (R$ 523,00) no mercado internacional. “Estamos tentando ajustes de porcentagens”, completa a diretora da Giroplastic.
FIBRA DE CARBONO
A Jacto também utiliza novos materiais na fabricação de máquinas agrícolas. A empresa produziu um painel de comando de um de seus pulverizadores utilizando polímero reforçado com fibra de vidro, o GFRB. O uso do polímero na construção da peça, que antes era feita de aço, teve como benefícios a otimização do design, maior produtividade, menor custo e melhor eficiência ambiental. Apesar de o GFRB não ser reciclável, como é o aço, ele permite a confecção de peças mais leves, que acarretam em menor consumo de combustível.
Além do painel de comando, todos os painéis de controle do sistema de aplicação dos pulverizadores Jacto são produzidos em plástico, assim como os abre-linhas e os paralamas. Há três anos, a empresa apresentou um conceito híbrido de 42 metros de barra de pulverização, construído em aço e fibra de carbono, que reunia a durabilidade e baixo custo do aço, além da leveza e resistência da fibra de carbono.
A barra foi desenvolvida para o pulverizador automotriz Uniport 4530, que, com o equipamento, teve um rendimento operacional de até 90 hectares por hora, sendo 12,5% maior se comparado com barras de 36 metros.
O índice de amassamento com barras de 42 metros foi 14% menor comparado com barras de 36 metros. “A máquina ficou mais leve, com melhor aceleração e frenagem, mais econômica e com menor compactação do solo”, destaca o gerente de negócio de pulverizadores automotrizes da Jacto, Rodrigo Madeira.
A empresa também usa polietileno e chapas de aço especiais na produção de peças para deixar as máquinas mais leves. “Se for comparar, as máquinas da Jacto são de 2 mil a 3 mil quilos mais leves que as da concorrência. Nós viemos substituindo o aço por materiais mais leves, focando na redução de peso, no meio ambiente e no melhor rendimento operacional”, completa.
BUCHAS AUTOLUBRIFICANTES
Cada vez mais as peças de desgaste (buchas, placas ou mancais autolubrifi- cantes) em polímero estão presentes nos grandes fabricantes de máquinas agrícolas. Na Igus Brasil, a tecnologia de componentes feitos em polímero de engenharia vem substituindo com sucesso soluções metálicas e os benefícios técnicos provenientes dessa substituição são muito perceptíveis no campo, aumentando a produção e performance do equipamento.
Essas peças são produzidas pelo processo de moldagem por injeção de plástico, podem ser customizadas por meio do processo de usinagem de barras do material de polímero de engenharia iglidur, ou por diferentes processos de impressão 3D. Denis Pereira, especialista da indústria agrícola da Igus, diz que seja qual for a tecnologia utilizada para a produção, os diferenciais técnicos dos componentes
em polímero de engenharia em material iglidur são os mesmos: peças livres de desgaste, livres da necessidade de lubrificação, vida útil prolongada e calculável de acordo com o ponto de aplicação e, consequentemente, uma maior disponibilidade das máquinas no campo, com produtividade superior.
Essas buchas e componentes em polímero de engenharia são mais econômicas e sustentáveis. “Com a utilização desse tipo de material, é possível eliminar o uso de graxas e lubrifi cantes utilizados nos pontos de articulações dos equipamentos e ter uma redução de custos, tanto no gasto com lubrificantes como no tempo antes gasto na lubrifi cação, em tempo de inatividade das linhas de produção/máquinas ou equipamentos”, afirma Lopes.
Os componentes em polímero também possibilitam redução do uso de combustíveis e energia em algumas aplicações por conta da leveza e eliminação/redução do atrito. Juntamente com a redução do peso, exige que me nos energia de acionamento seja utilizada para mover uma peça. Outro ponto é a durabilidade e vida útil. “Esses componentes são otimizados para o desgaste, livres de corrosão e duram cerca de quatro vezes mais do que os componentes metálicos, resultando em menor substituição”, diz.
MANGUEIRAS PREMIUM
A Gates Brasil busca a ruptura de conceitos dentro da “ciência dos materiais” trazendo para seus produtos a redução de aplicação de matérias e inovando na busca de materiais e compostos mais leves e menos agressivos ao meio ambiente. Em suas atividades de pesquisa e desenvolvimento é obrigatório a utilização de novos materiais com o conceito Chloroprene Free. “Esse tipo de composto vem sendo aplicado nos novos desenvolvimentos e nas composições atuais de borracha que a Gates utiliza ou aplica globalmente e faz parte dos requisitos das grandes montadoras globais”, afirma o gerente de produto Reposição, Frederico Muller.
Para o segmento de correias, a Gates está introduzindo produtos utilizando o EPDM, tecnologia utilizada em ampla escala e diversidade há alguns anos na Europa e nos Estados Unidos. “Esse tipo de material proporciona melhor desempenho e durabilidade em aplicações severas, em que a temperatura e a maior resistência à abrasão são pontos primordiais nos requisitos dos montadores e suas aplicações em tecnologias avançadas em seus sistemas e equipamentos”, salienta.
No segmento de transmissão de potência por fl uídos, a Gates desenvolveu a linha de produtos Mega X, com avanço na tecnologia dos materiais, e ampliou o conceito com as linhas de mangueiras hidráulicas premium MXT e MXG. A MXT, fabricada com um só trançado de arame mais compacto, é 30% mais leve, o que refl ete em maior rendimento, menor consumo de combustível e economia na logística. Ela também é mais flexível e requer, em média, 40% menos força para dobrar. O produto é certificado para 600 mil ciclos de impulso, três vezes mais que as normas SAE e EN.
Para linhas tradicionais de mangueiras espirais, a Gates inovou com uma mangueira trançada, com qualidade superior. A MXG é mais leve, fl exível e compacta e com performance de 1.000.000 de ciclos deimpulso. “Substituímos as mangueiras de reforço em espiral por mangueiras com o novo conceito Xpiral, em que os equipamentos utilizados na fabricação entregam um reforço que, com apenas duas camadas de fi os de aço, atendem o mesmo desempenho e durabilidade das mangueiras com quatro espirais.”
IMPRESSÃO 3D
A Cummins Brasil considera diversos tipos e opções de materiais avançados, além de tecnologias de impressão 3D capazes de imprimir peças metálicas, como alumínio e peças fundidas, além de peças plásticas (compósitos).
“Para o mercado de reposição e/ou para itens de baixo volume de produção, em que temos um elevado custo de desenvolvimento do ferramental para produção das peças, temos avaliado o uso da impressão 3D, uma vez que prezamos pela qualidade e confi abilidade, além de garantir o fornecimento de peças, de acordo com os requisitos dos nossos clientes”, afirma o gerente de Engenharia de Produto da Cummins, Renan Barro.
O executivo diz que para componentes com materiais metálicos e que possuem características estruturais (solicitação mecânica), a tendência está na utilização das impressoras 3D com capacidade para a fabricação de materiais metálicos ou com resistência mecânica similar.
A Cummins tem investido na construção do próprio ferramental por meio da impressão 3D. “Essa prática tem trazido cada vez mais a redução da quantidade de material necessário para a produção das peças, bem como do próprio ferramental, trazendo benefícios, inclusive, para o meio ambiente, minimizando o descarte”, observa. Nos casos de componentes como baixa solicitação mecânica, a companhia tem avaliado e, quando possível, substitui as peças metálicas por peças plásticas. Um exemplo são as
conexões de entrada e saída de água.
“Com a impressão 3D podemos identifi car, de forma rápida, possíveis problemas de interferência com componentes adjacentes, seja no próprio motor ou até mesmo da máquina, bem como problemas de acesso ao operador que fará a montagem do item na linha de produção, assim como no caso de uma manutenção preventiva e corretiva por parte dos concessionários e usuários fi nais”, finaliza.